Pre-Coat Filter filtration to sub-micron range
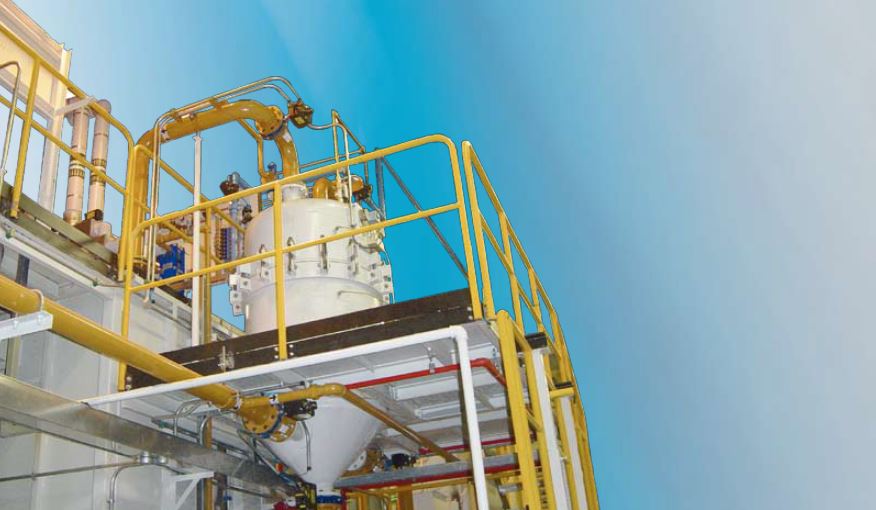
Overall System Design
A complete automatic cycling Pre-Coat filtration system consists of the Pre-Coat filter vessel, a patented slurry feeder for mixing and storing the pre-coat material, a Hydro-Vac secondary recovery filter to concentrate and remove the dirt Ioaded pre-coat powder after each filtration cycle and a main system liquid reservoir.
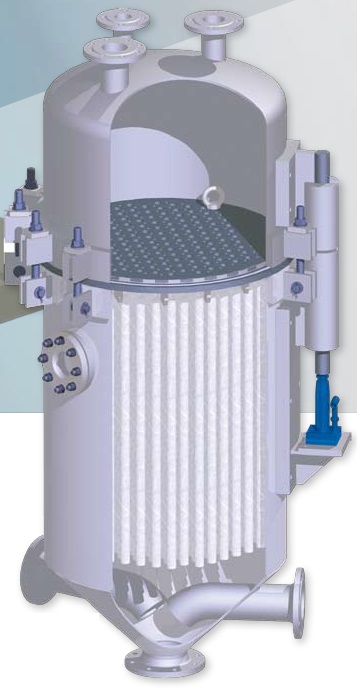
The Primary Filter
The heart of the Pre-coat filtration system is a pressure vessel containing a packed array of wire-mesh-covered, perforated tubes. The tubes are attached to a basee in the upper dome structure of the vessel. Fabrication of this assembly is such that any liquid flow, in either top-to bottom or bottom-to-top direction, must flow through the perforated tubes.
The mesh-covered tubes serve as septums upon which a fine cellulose powder (or an alternative filter aid) is deposited in thin layers to form a filter cake. This filter cake permits removal of contaminant particles as small as 1/2 micron. When cellulose powder is caked on the filter septums, it becomes an excellent ultra-high filtration medium which permits liquids to flow through the microscopic pores in the cake, but prevents the passage of suspended solids (i.e. contaminants). In the filtration mode of operation liquid flows vertically up through the pre-coated filter tubes into the pressure vessel
dome. From there the filltered liquid is transported to a clean liquid storage tank.
The slurry tank is a steel reservoir used for mixing clean liquid with filter aid to create the pre-coat slurry. A storage hopper and feeder are mounted on the slurry tank.
The secondary filter is generally a Hydro-Vac vacuum filter. However, a Flat Bed pressure filter may also be used on special applications. The Hydro-Vac unit concentrates and removes the dirt-laden pre-coat powder following each filtration cycle.
The main system liquid reservoir is a divided tank. One compartment holds dirty liquid discharged from the operation; the other holds clean filtered liquid to be re-circulated. The tank may be equipped with a drag conveyor and/or magnetic separator if the liquid contains solid that can be readily removed by settling. The reservoir may also be a simple, vertical-sided tank for systems requiring the removal of only fine particles.
The coded pressure vessel is designed and fabricated to withstand the highest expected pressure it will encounter with a safety factor of three. For installations requiring special certification, vessels will meet the requirements and stamped accordingly.
The pre-coat storage hopper is designed to accurately meter a hygroscopic powder, like cellulose, regardless of humidity levels.
Animation
Automatic sequence of operation
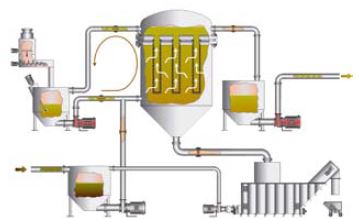
1. FILTER-FILL
When the filter-fill operation starts, the primary filter vessel is empty, the tubes are clean and the recovery system is isolated. Clean liquid is pumped into the primary filtering vessel from the slurry tank filling the vessel entirely.
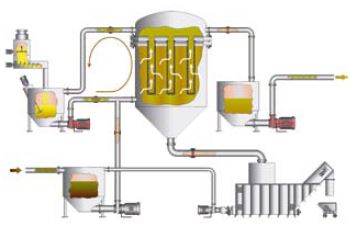
2. SLURRY MIX
As clean liquid is circulated from the primary filter back into the slurry tank, a hopper meters filter-aid powder into the slurry tank, mixing it with clean liquid and creating a precoat slurry.
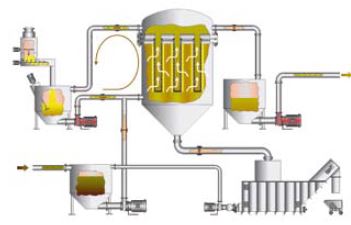
3. PRE-COAT
As the slurry is pumped into the bottom of the primary filter vessel it flows up through the tubes and back to the slurry tank. Repeatedly re-circulating this slurry deposits a full layer of filter powder on the outside of the tubes (screened surface).
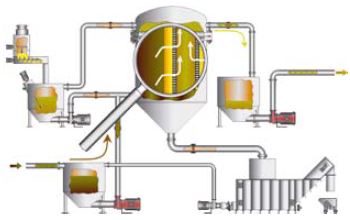
4. FILTER CYCLE
When the screened tubes are pre-coated, the filtration process begins automatically. The following actions occur simultaneously: the filter pump feeds dirty liquid to the primary filter and the slurry pump is stopped and the slurry feed valve is closed. The dirty liquid flows through the intricate micro passages of the pre-coat filter cake where particles down to 1/2 micron and smaller are retained. The filtered liquid travels up the perforated tubes to the upper chamber of the primary filter and is then transferred out the clean liquid return line.
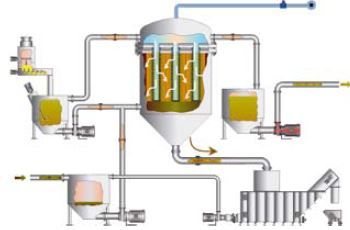
5. BLOW-DOWN -SYSTEMS
BLOW-DOWN IS TRIGGERED AUTOMATICALLY
As contaminants build up on the filter cake, the pressure dierential between the top and the bottom of the main filter vessel gradually increases. At a preset pressure level blow-down begins. All feed and discharges valves are closed and a large dump valve opens. Compressed air enters the primary filter dome, forcing the clean liquid down and through the perforated tubes. The blow-down force is such that all liquids, pre-coat powder and contaminants are effectively discharged from the primary filter tank and into the secondary recovery system in approximately 12 seconds. This rapid discharge effectively cleans the primary filter tubes and the next pre-coat automatically begins.
RECOVERY FILTRATION
When the blow-down cycle is completed, the small Hydro-Vac filter begins operation. A negative pressure in the Hydro-Vac draws the liquid in the dump tank, down through a filter cloth where contaminants and pre-coat powder are deposited. The Hydro-Vac filter operates until all liquid has been removed from it and all used pre-coat powder and dirt are deposited in a bin. The secondary filter then shuts down until the next blow-down cycle.
Examples

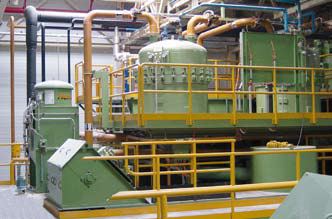